Niobium for high carbon wire products
High carbon steel wire rod is a semi-finished product. Further processing, by techniques including cold drawing, cold rolling, cold upsetting, then produce several different end products such as wire ropes for bridges and prestressing steel wires for prestressed concrete in civil engineering construction and
structures.
For some applications they have to reach very high tensile strength levels, higher than 2,000 MPa, that can be reached by dry wire drawing from diameters around 5.00 to 7.94 mm to final diameters from 0.15 to 0.40 mm. Due to this intensive steel work hardening during drawing, the material has to be submitted to intermediate patenting treatment, getting back its capacity to be cold drawn again. These wires are submitted to strong stresses during drawing, that can cause breakage with a strong decrease of productivity and the reduction of final wire quality. The addition of up to 0.025% Niobium for these products helps to improve the so called drawability of wire, reducing these breakages and minimizing the need of the intermediate patenting treatments.
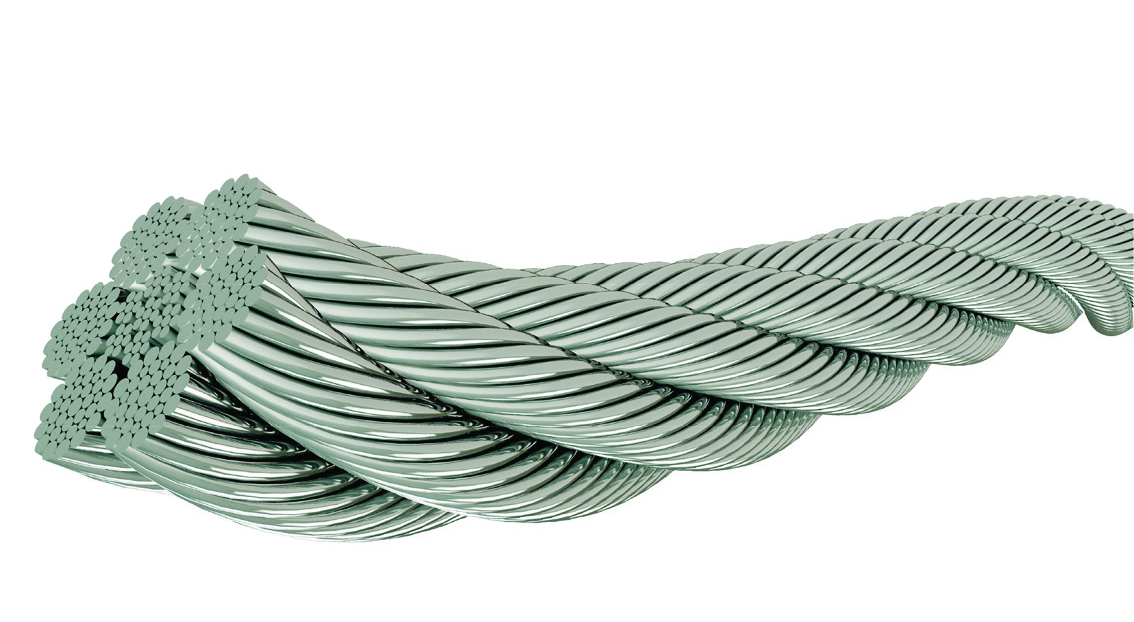
Figure 1: Example of high carbon steel wire rod finished product
An industrial heat was produced at an integrated BOF melting shop operation for 0.83% C wire rod steel. Steels with and without 0.018% Nb were compared during operational wire rod drawing.
Table 1: Chemical composition of high carbon with and without Niobium tested during an industrial heat


MicroNiobium Steelmaking Alloy Approach in 1080 Wire Rod. S. G Jansto; Association for the Iron and Steel Technology - Oct. 2014
A wire rod with 7.5 mm was drawn to 2.4 mm in different wire manufacturers and no annealing was required to reduce 90% of its cross-sectional area
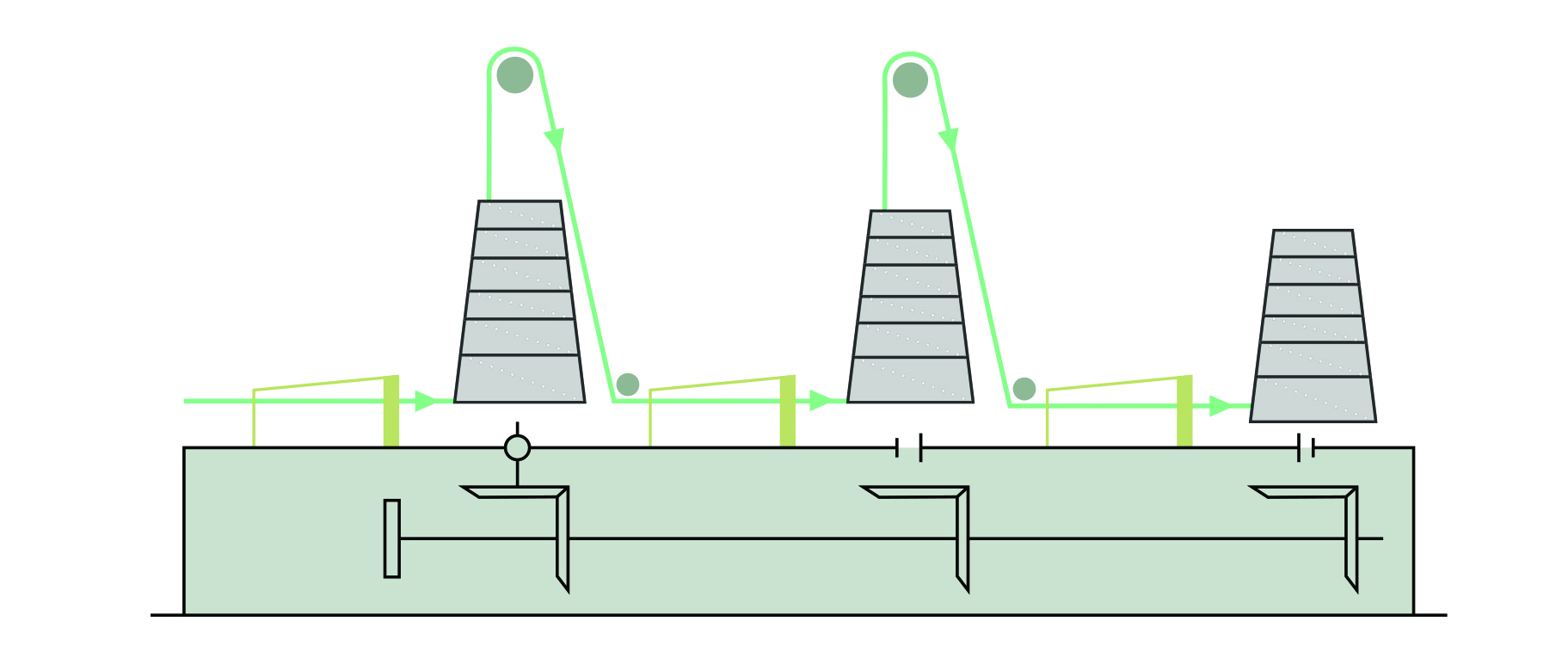
Figure 2: Scheme of a tandem drawing machine
Adapted from http://www.idc-online.com/technical_references/pdfs/mechanical_engineering/Wire_and_bar_drawing.pdf
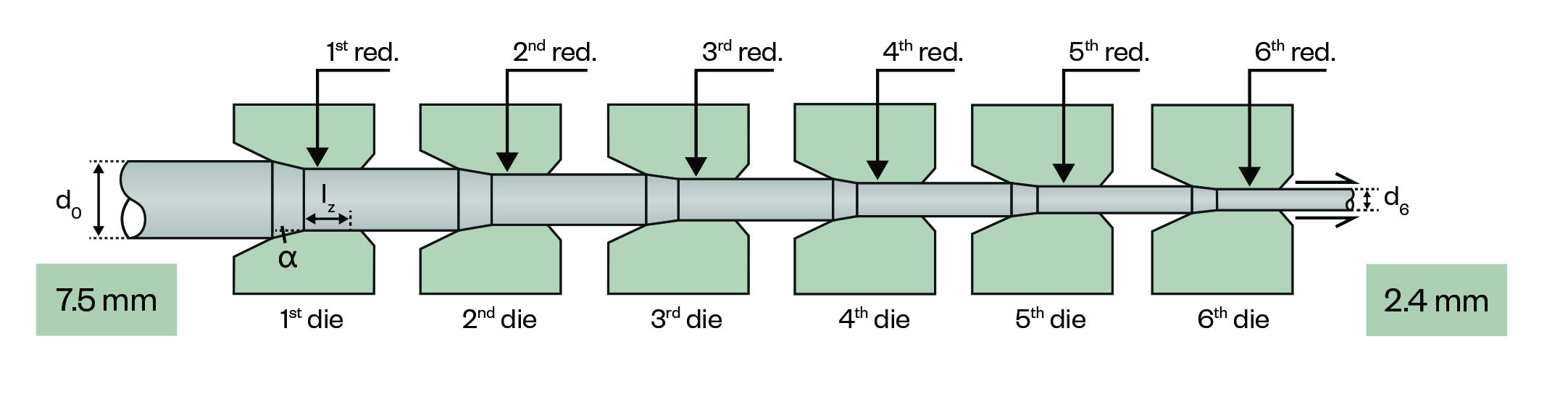

Figure 3: Schematic presentation of the cold drawing process from 7.5 mm to 2.4 mm with multiple passes through the dies. Adapted from Structural integrity of progressively cold-drawn pearlitic steels: from Raffaello Sanzio to Vincent van Gogh. Science Direct - Procedia Structural Integrity 3 (2017) 3-10.
During the drawing operations, the Niobium wire rod presented higher ductility if compared with non Niobium wire rod
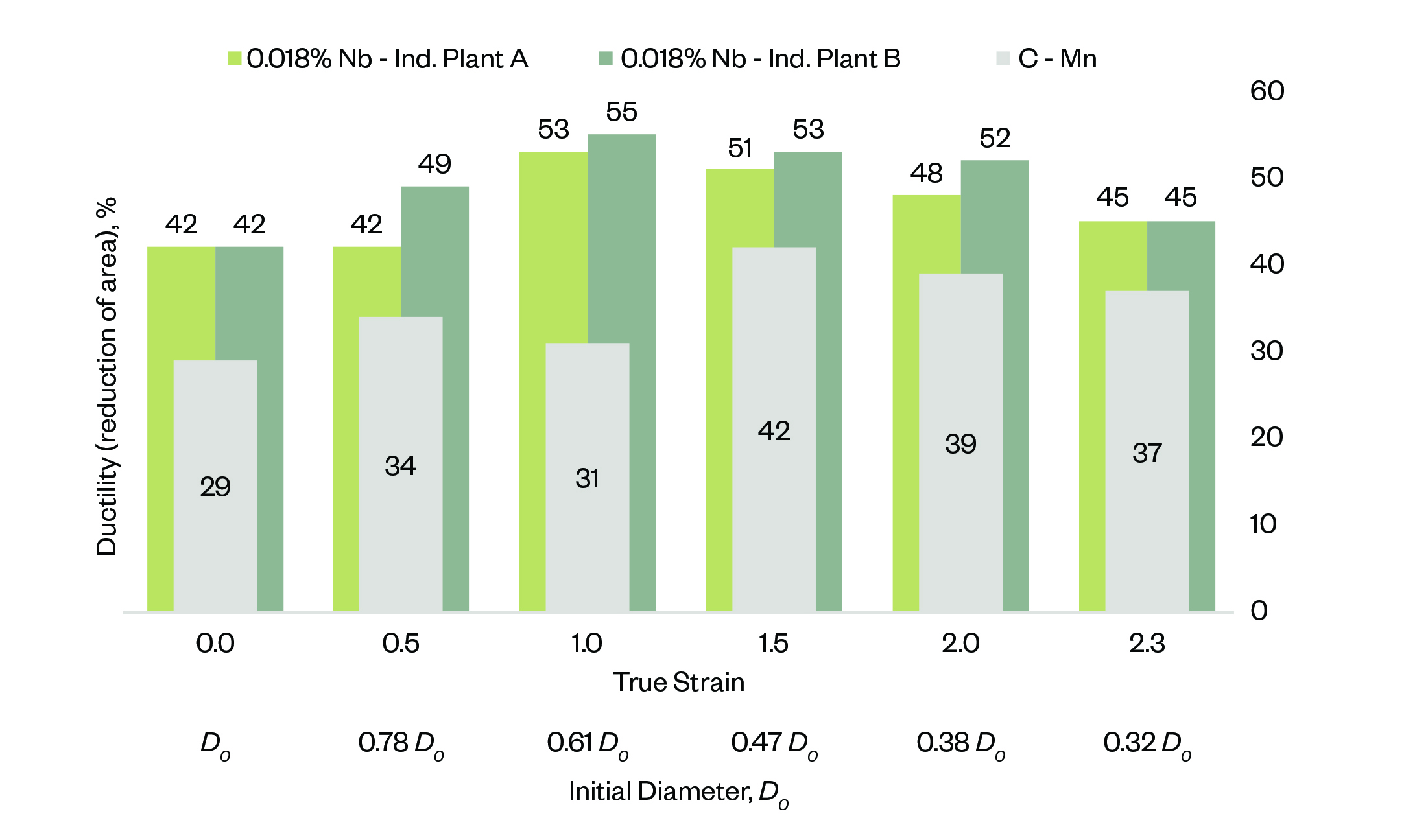
Figure 4: Relation of reduction as a function of strain applied during drawing process, pointed by the reduction of diameter of wire. For instance, the 1.5 true strain represents the value as 0.47D0 expressed as a function of the initial diameter. Adapted from MicroNiobium Steelmaking Alloy Approach in 1080 Wire Rod. S. G Jansto; Association for the Iron and Steel Technology - Oct. 2014
The most important parameters for evaluating the wire’s ability to be drawn are:
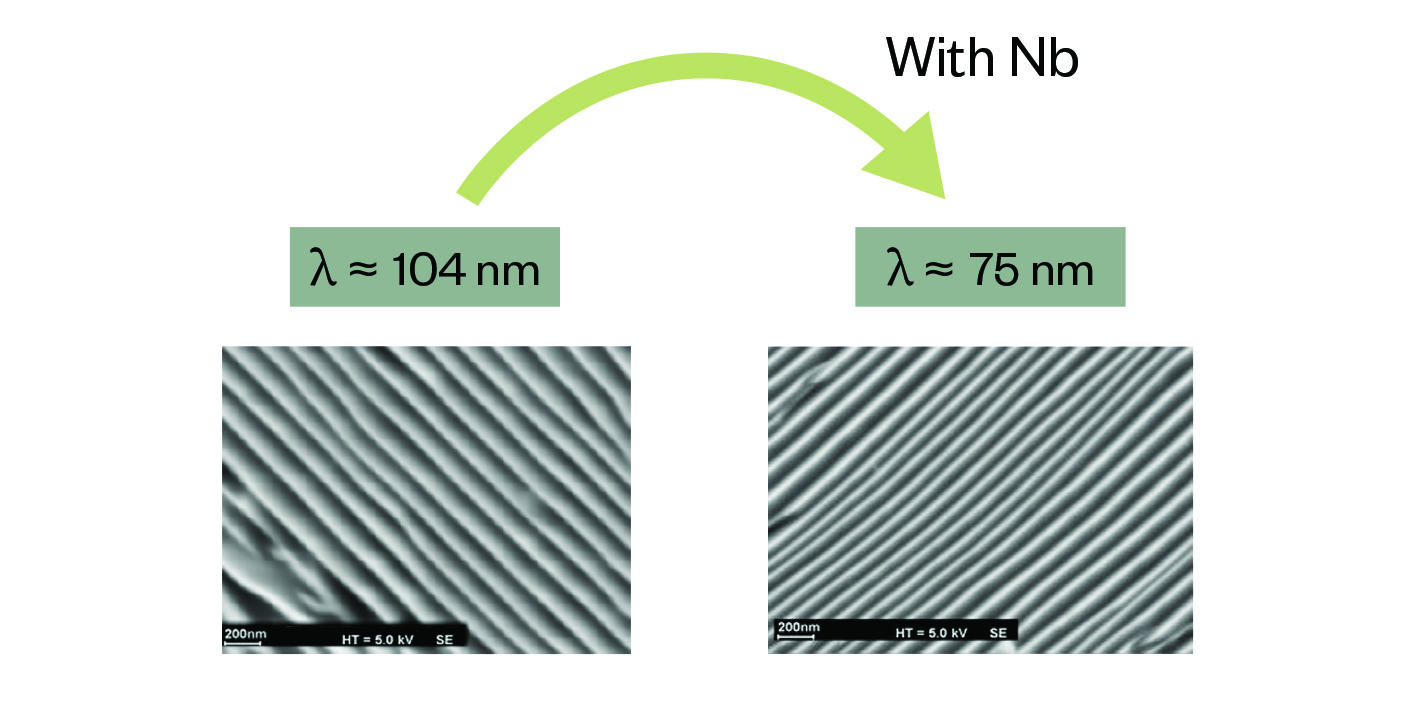
Figure 5: Refinement of pearlite interlamellar spacing by adding 0.018%Nb at 0.83%C steel wire rod. Adapted from MicroNiobium Steelmaking Alloy Approach in 1080 Wire Rod. S. G Jansto; Association for the Iron and Steel Technology - Oct. 2014
The refinement of pearlite interlamellar space can be estimated assuming that both ferrite and cementite plates undergo the same strain and the interlamellar spacing is reduced proportionally to the wire diameter during wire drawing, as per equation:
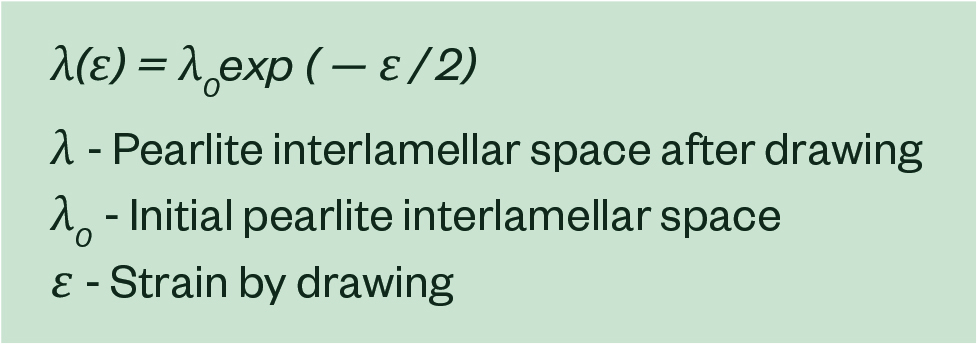
Figure 6 shows the refinement of pearlite interlamellar space during the drawing process. The steel with Niobium has finer pearlite during the process, explaining its better capacity to be drawn. The finer pearlite reduces the need for intermediate heat treatments, in order to recover the steel capacity to be drawn, which then guarantees the high productivity of the process.
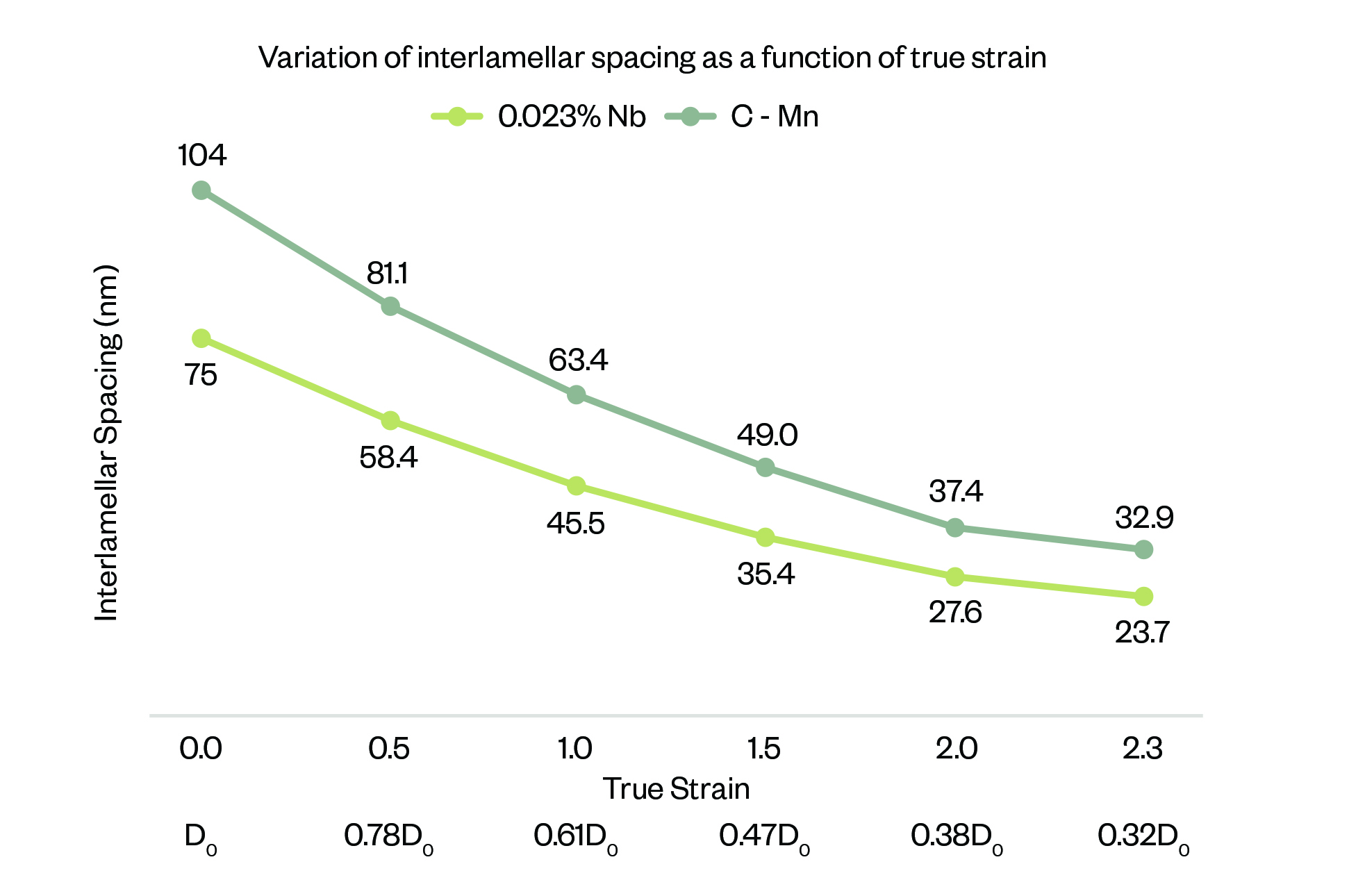
Figure 6: Refinement of pearlite interlamellar spacing during drawing for Niobium and non-niobium 0.83%C wire rod. Adpated from Effect of microstructural features on ductility of drawn pearlitic carbon steels. Won J. Nam, Hyung R. Song and Chul M. Bae; ISU International, vol. 45 (2005) no.8, 1205-1210
Relying on high carbon wire with Niobium to deliver superior products to a global market
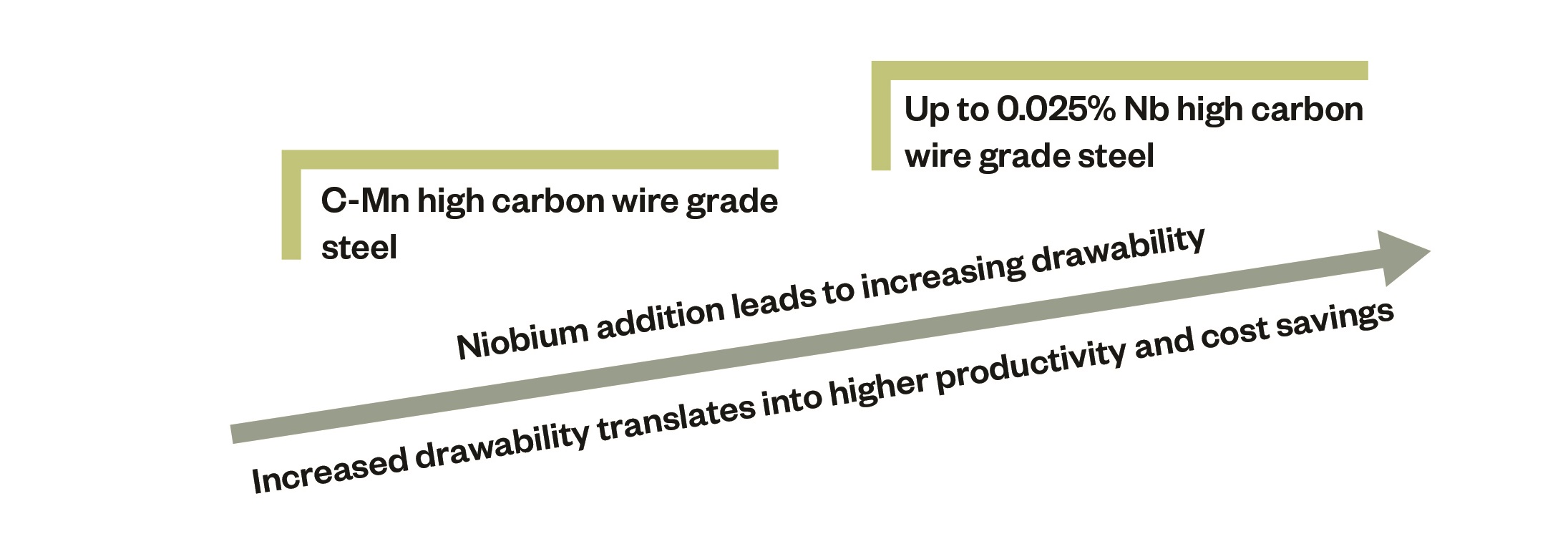
MicroNiobium Steelmaking Alloy Approach in 1080 Wire Rod. S. G Jansto; Association for the Iron and Steel Technology - Oct. 2014
Want to see this content in another format?
You may also like: