This article was originally published on the March 2021 issue of the Stainless Steel World Magazine.
Readers of this article probably already know that stainless steels are versatile and modern materials. When I’ve discussed the properties of stainless with colleagues not fully involved in this industry, the first thing that came to their minds is corrosion resistance, beautiful surface quality, and higher prices compared to other types of steels. This is unfortunate, as stainless steels are widely utilised for other characteristics as well. These include high-temperature performance, fire resistance, antibacterial applications, high mechanical stress, and suitability for high-pressure applications and even aerospace.
The pre-conception that stainless steel is a high-cost material has unfairly hindered or slowed several industry developments and opportunities in the last decade. Hopefully, by the end of this article, you will have a different perspective on how the industry can work together in a cooperative approach to give stainless steels the chance to promote all its advantages and be the material of choice for the near future.
New applications and products are an exciting topic to discuss, particularly the disruptive ones that will change our lives. The major aspects that come to mind in these discussions are cost efficiency, technical advantages, industrialisation, and implementation time for the new solution. While these are important indicators, considering the cost of material and not the cost of the solution is the biggest single mistake that can jeopardise the development of stainless steels.
Although in many cases the material may be more expensive compared to the original solution, the technical benefits gained by its usage can increase the lifetime of the component or even optimise its manufacturing process, bringing positive outcomes to the cost of the final solution and the overall cost of the component.
Two branches of developments
Two branches of development are growing and gaining momentum in the stainless steels industry. The first is linked to the replacement of materials, focusing on sustainability, technical advantages, and the cost of the solution. By contrast, the second branch focuses on substituting one stainless steel alloy for another, often optimising the solutions costs, sustainability aspects and the technical performance. Both strategies are addressed in this article, and a common methodology to deal with both will be explored.
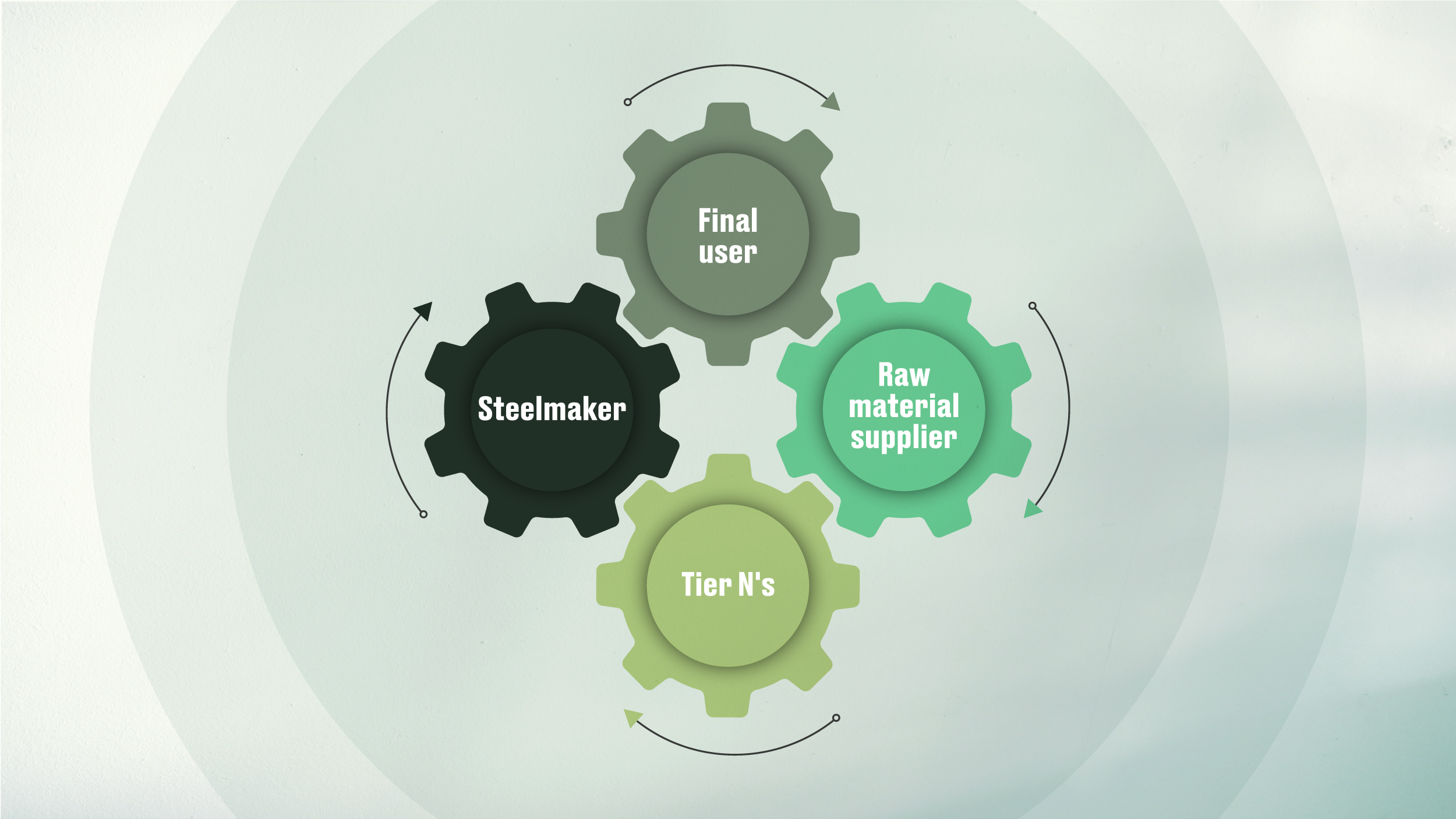
Example of the circular approach
Developing stainless steel solutions for applications that have traditionally used different materials is complex. However, it is an important topic for modern engineering, as it requires a multi-disciplinary approach. In many cases, a metallurgical development at the plant will be necessary to optimize the steels’ alloy and microstructure. In addition, intervention on the in-use properties and manufacturing process of the end-users will also be necessary to adjust welding, stamping and other process parameters.
In this situation, a circular approach is the most optimal solution. From the beginning of the development process, the whole manufacturing chain is involved in a single project, from the raw-material supplier and stainless steel producers to the Tier Ns and end-users. This will speed up the development process, avoid wasting resources and prevent developing a solution unacceptable to the end-user.
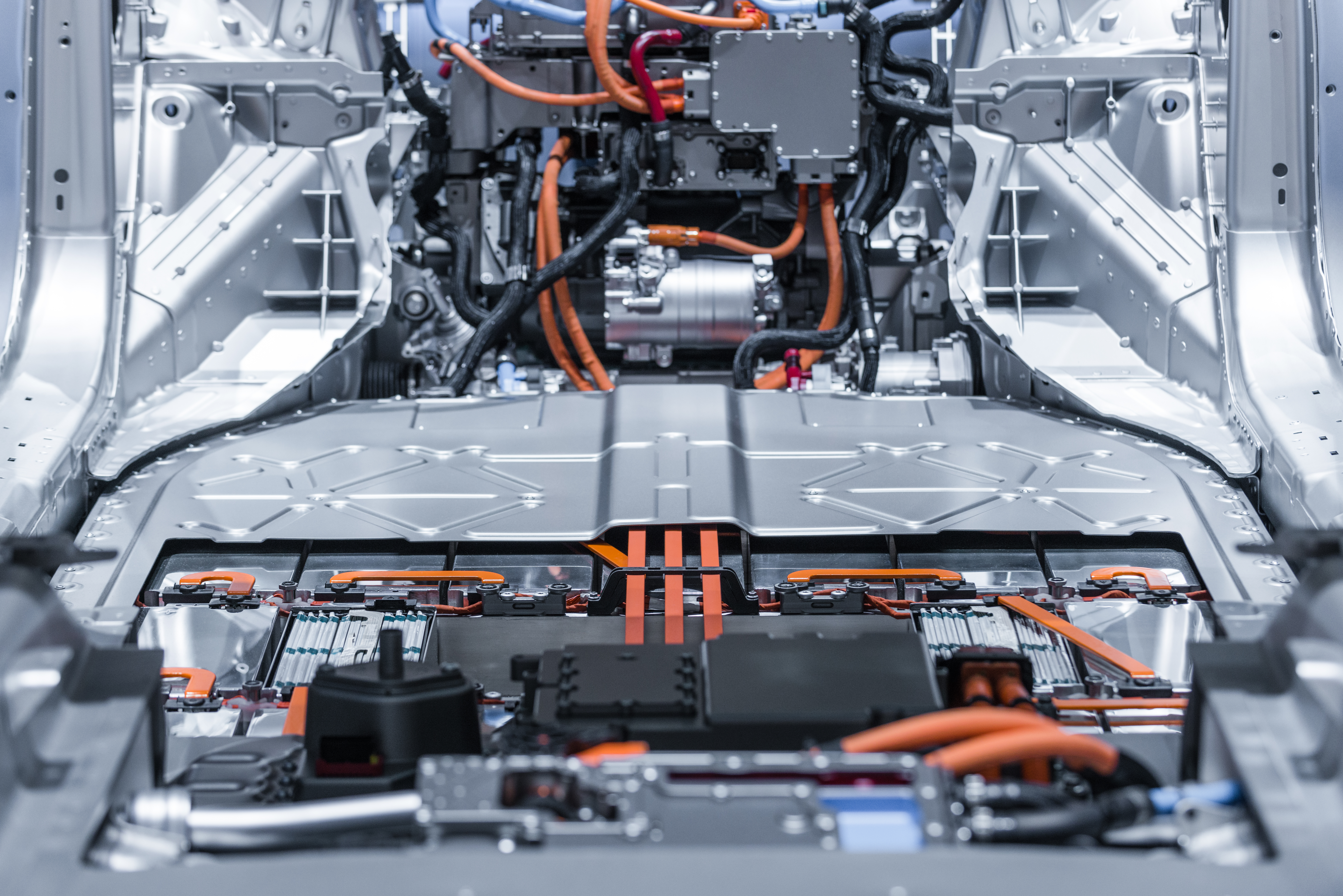
Substituting flat aluminium components in the battery pack of electric vehicles for stainless steels has resulted in extra fire protection, mechanical performance, and corrosion resistance.
Successful examples can be highlighted, such as developing stamped manifolds in automotive exhaust systems to substitute cast iron manifolds. Stamped manifolds considerably reduced the components’ weight while increasing vehicle performance, reducing emissions, and enhancing in-use performance with alloying strategies. These strategies included the addition of Niobium in the chemical composition to increase fatigue and high temperature performance.
Maintaining the mechanical properties while avoiding creep phenomena are crucial characteristics for the component and increases catalysis efficiency.
Another recent example to be highlighted is the substitution of flat aluminium components in the battery pack of electric vehicles for stainless steels covers. It has allowed OEMs to find an interesting correlation between fire protection and mechanical performance with low thicknesses and corrosion resistance, while removing the need to e-coat the component necessary for carbon steel.
Returning to the second branch of development - substituting one stainless steel alloy for another - it is possible to see that the industry has dealt with this a lot over the years. Some market trends are good catalysts to promote this change, one of the foremost being the nickel price, and we’ll explore this a little bit more.
Nickel as a catalyst for change
The price of nickel is well-known for its instability. In 2007 it reached over USD 50,000 per ton and two years later dropped to around USD 9,300 per ton, according to the London Metal Exchange (LME). This volatility creates huge uncertainty for stainless steel final users, as a major portion of a materials price is an alloy surcharge. If the nickel price rises during the production of an austenitic grade, the purchase price will also rise, directly affecting the end-users financial results. Some financial institutions reinforce that the threshold value of nickel price to unlock investments in the industry is USD 20.000 per ton. We are close to this price at the moment, due to tensions between Southeastern Asian suppliers and the European Union.
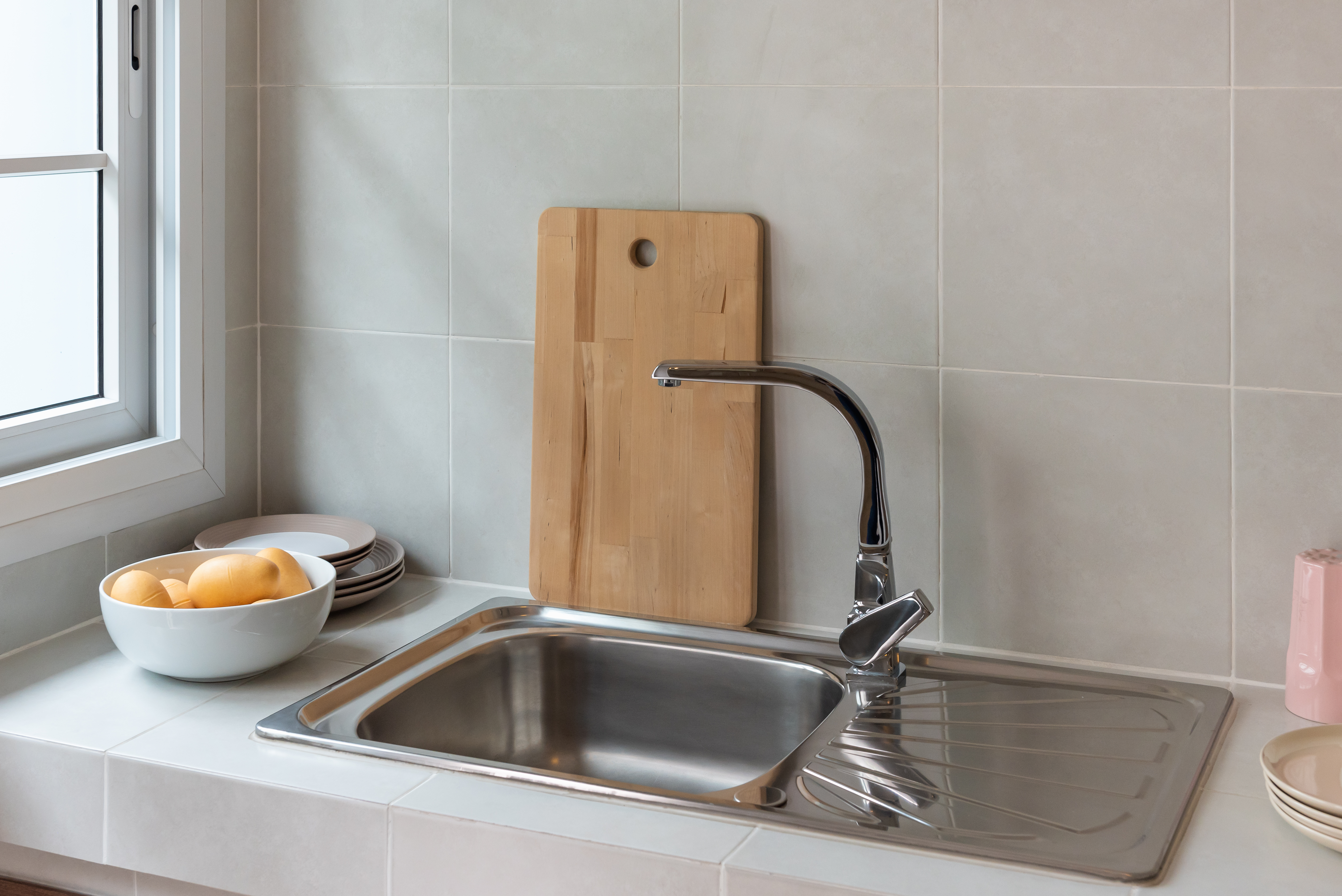
The development of a special ferritic grade allowed it to substitute austenitic stainless steel for kitchen sinks.
New grades gaining ground
Returning to the circular approach, very good results can be obtained when the main players in the manufacturing chain work together. Alloying and steel making process strategies can enhance the metallurgical properties of a material. Adjustments in the manufacturing process can be applied to improve the weldability and formability of ferritic steels.
One prominent example is the substitution of austenitic stainless steel sinks for ferritic stainless steel sinks. This was only made possible by developing a special ferritic grade, with Niobium and other chemical elements in the composition. A special process route was also developed, whereby the crystallographic texture and anisotropy of the material reached very interesting levels. At the end-user, special adjustments were made to the stamping process, by reducing the blank holder pressure, alleviating the die radius, increasing lubrication and adjusting the blank design. It is also important to mention that swapping austenitic grades for ferritic grades can positively affect the solution’s carbon footprint since we are removing nickel from the equation.
For many applications where surface quality and corrosion resistance are crucial, alternative grades have gained ground, such as duplex and molybdenum ferritic materials, which have replaced standard austenitic steels. Today, the doors and internal panels of many elevators are produced in DIN 1.4509 (441), UNS S43932 and even AISI 444. The same is true for industrial kitchens, white goods and architectural applications. For this last application, there are two important examples of soccer stadiums in Brazil, the Allianz Parque and the Arena Castelão, built for the 2014 FIFA World Cup.
The energy industry has also witnessed some modifications in the last decade, with austenitic grades or other alloys losing ground to stabilised ferritic stainless steels with high thermal conductivity for heat exchangers. As they are stabilised with titanium, Niobium or even dual-stabilised with both, they can be easily welded and formed.
It is clear that the stainless steel industry has evolved a lot over the years and that technology has followed this evolution. Production volumes have risen in the last decade, particularly in Asian countries where most stainless production occurs. So I would like to conclude this article with a provocative reflection: stainless steel is a centenary material, really versatile and capable of adapting to complex environments. This is not so different than the moment that we are living in right now, so why don’t we inspire ourselves with the material that we work every day and also try to optimise developments by working in a more sustainable and integrative way?
To read the entire March 2021 issue of the Stainless Steel World Magazine.
Want to see this content in another format?
Podcast to learn more