The use of low carbon concept steels with Niobium levels up to 0.11% improves linepipe weld zone properties both during pipe manufacture, using submerged arc welding (SAW), and during site girth welding with lower heat input processes such as gas metal arc welding (GMAW). These significant benefits derive, primarily, from the heat affected zone (HAZ) grain coarsening resistance of such steels during the welding process.
The heat affected zone (HAZ)
The microstructure which develops in the heat affected zone (HAZ) immediately adjacent to the weld is a function of many variables.
These include steel composition, plate or coil thickness, welding process selection, heat input, welding speed and the number of weld passes.
All of these factors influence the heating and cooling rates during and following welding. Ultimately, all these variables determine the grain size which develops in the coarse grain HAZ and dictate the mechanical properties of this important region.
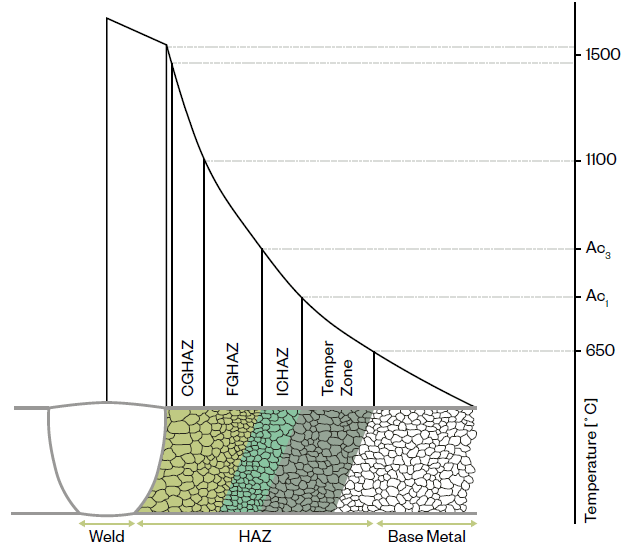
The role of Niobium in the HAZ
Niobium is the key element but with additional minor microalloying using titanium, complex very fine precipitates are generated in the steels which control grain coarsening of the HAZ during the welding process. This effect is maximised over a wide range of heat inputs when Niobium is in the range 0.08 to 0.11%. This important effect, combined with other unique attributes of Niobium in solution, ensures the development of optimum HAZ microstructure and toughness in all conditions of interest both in pipe fabrication and during subsequent girth welding.
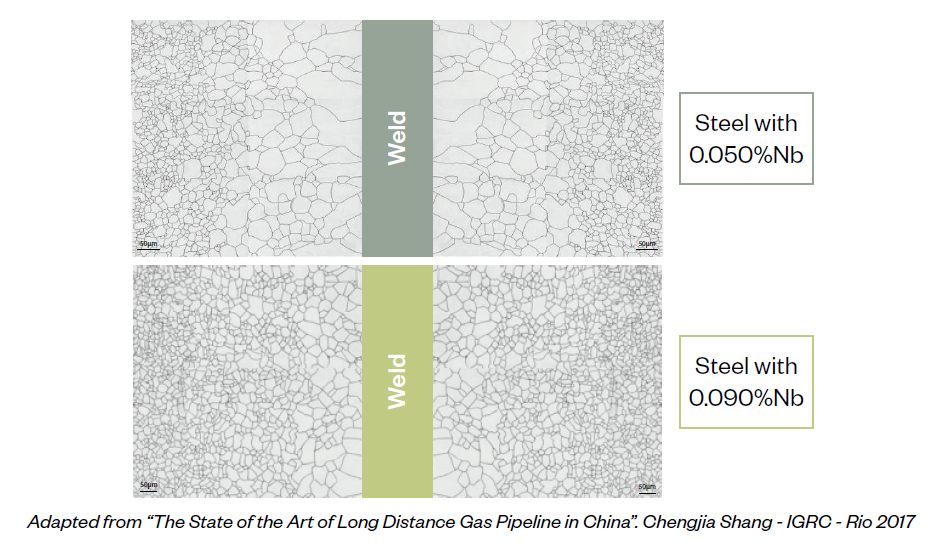
This refinement can be further appreciated using Electron Back Scattering Diffraction (EBSD) on the welded joints of the following steels.

EBSD images show the microstructural variation from weld metal to base material in steels A and B.
The paper from which these images are reproduced shows that the increase of Niobium content from 0.07% to 0.10% combined with an appropriate ‘best practice’ rolling schedule has ensured the generation of an optimum precipitate size distribution in steel B with the higher level of Niobium.
This has reduced the extent of the coarse grain HAZ (CGHAZ) from 275 um in the 0.07% Nb steel to 125um in the steel with 0.10% Nb. These finer grains in the CGHAZ result in a finer microstructure (finer packet size).
Niobium effect on base metal and heat affected zone microstructure of girth welded joints.
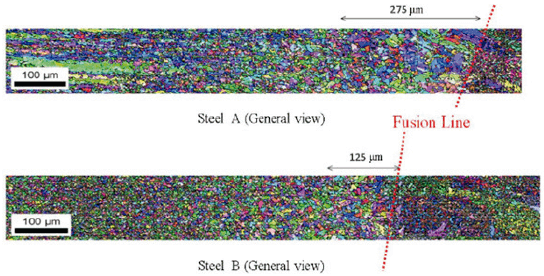
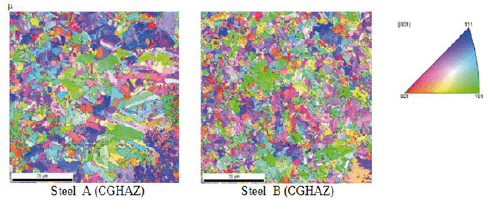
Andrea Di Schino, Paolo Emilio Di Nunzio, Acta Metallurgica Slovaca, vol. 23, no.1, 2017
Other supporting results of the Niobium effect on HAZ
The increase in weld heat input directly correlates with an increase in deposited weld metal and therefore overall weld productivity.
The toughness of 0.11% Nb steel is less dependent of the heat input of welding.
Barbaro, F et al. Development in the Control of Weld HAZ
Properties in Modern Microalloyed Steels, SEAISI Convention &
Exhibition, Vietnam, 2016
Niobium and titanium promote grain refinement in the CGHAZ. The effect is very pronounced when Niobium content is in the range of 0.08 to 0.11%.
The direct consequence of austenitic grain size control and the resulting microstructural refinement in the CGHAZ of the higher Niobium steel is enhanced toughness.
Qingyou, Liu. “The Alloy Design and Weldability of High
Performance Pipeline Steels”. Int’l Conf, on Pipelines and Linepipe
Steels (ICPLP), Xi’an China, April 2015.
Further evidence that 0.08% Nb steel is less sensitive to the welding heat input
Data from CBMM Collaborative program with TsNIIChermet [I P Bardin Institute] Moscow, Russia. The data in the following table and figure is adapted from the publication cited below and describes the welding performance of the two production linepipe steels.

The effect of using a higher Niobium content on the CGHAZ Charpy Toughness at different test temperatures and different cooling rates.
Frantov et al., ‘The Effect of Alloying and Microalloying Additions on Base Metal Properties and Weldability of X70/X80 Linepipe Steels’. Proceedings of the International Conference, Microalloyed Pipe Steels for the Oil and Gas Industry, Moscow, Russia, 2013.
The data confirms the significantly greater flexibility and tolerance to increased heat input of the higher Niobium steel over the full range of practically relevant cooling rates. A heat input of 10 kJ/cm, as might be encountered in Gas Metal Arc Girth Welding (GMAW), of thick-walled pipe >20mm wall thickness would result in a t (800-500) of <5 secs whilst pipe mill multi arc submerged arc welding on the same material might have a heat input in the range 40 to 50 kJ/cm resulting in a t (800-500) in the range 50 to 90 secs.
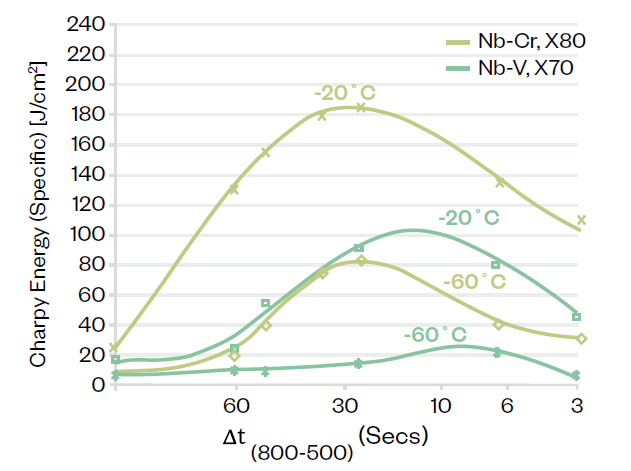
Proven results in actual pipes
Example 1: 1,219 mm diameter, 23.7 mm thick pipes, produced with ArcelorMittal X70 steel using Niobium content above 0.08%.
Both welds SAWH and GMAW presented excellent properties.
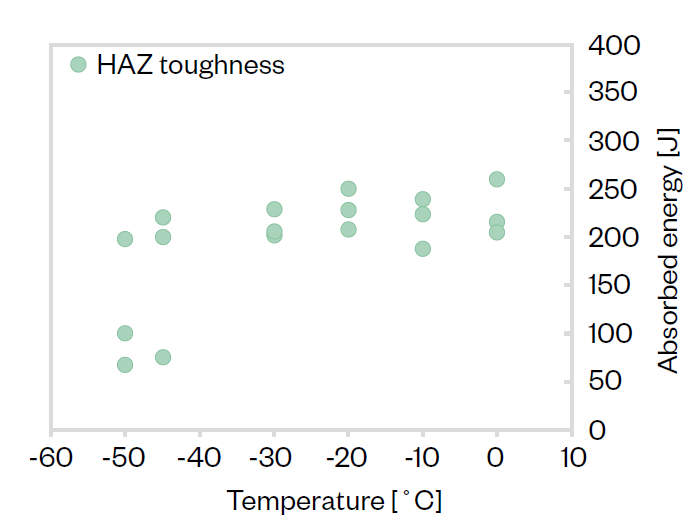
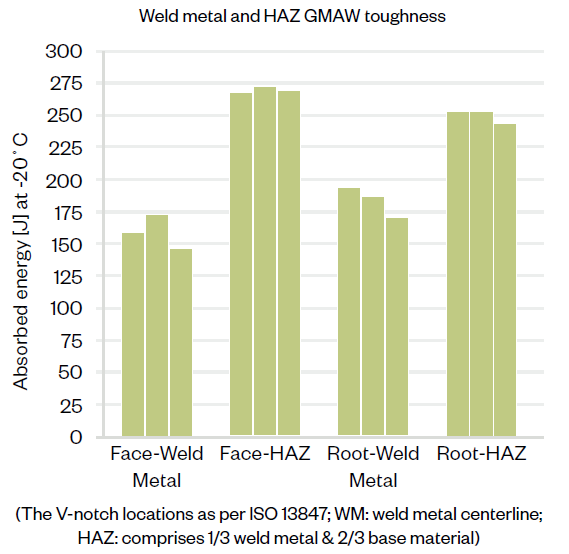
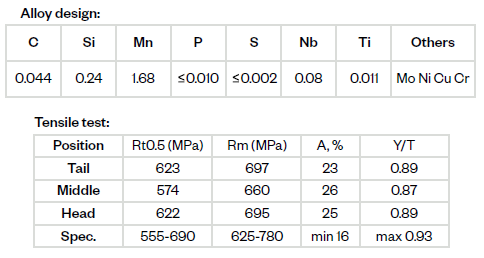
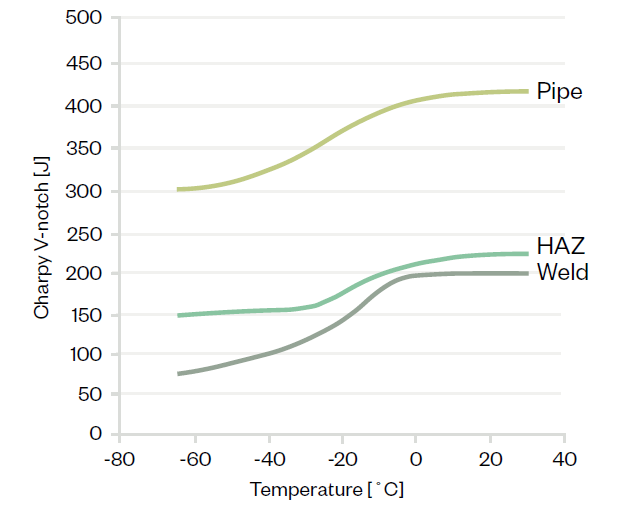
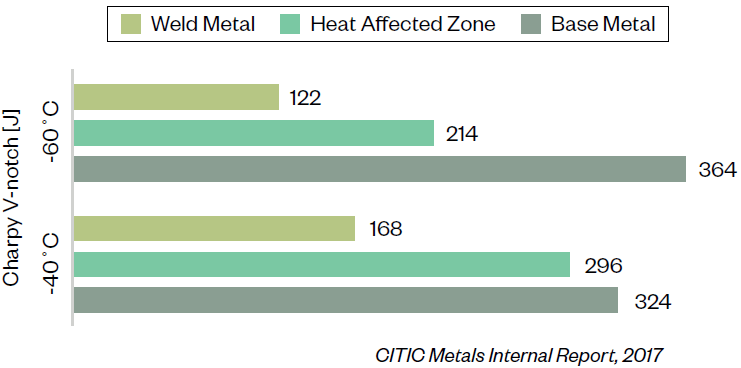
Want to see this content in another format?
You may also like: